Accidental contact with live equipment is the #1 cause of injury for electrical workers. The safety pros at EPSCO have performed numerous case studies and know that many workplace fatalities could be avoided with better safety procedures.
To build the best safety practices for your team, start by conducting an electrical safety task audit. A task audit is a step-by-step analysis that will help your safety team gain knowledge of your facility.
During an electrical safety task audit, your team will:
- perform checks on equipment
- identify hazards
- ensure qualified workers are current with codes and equipment
Every piece of equipment in your facility should be audited and ID’d. Begin by assessing the equipment for hazards, noting the recognized hazards, then determining hazard mitigation strategies. The Hierarchy of Risk Controls is a six-level system of controls that you can use to develop practical hazard mitigation strategies.
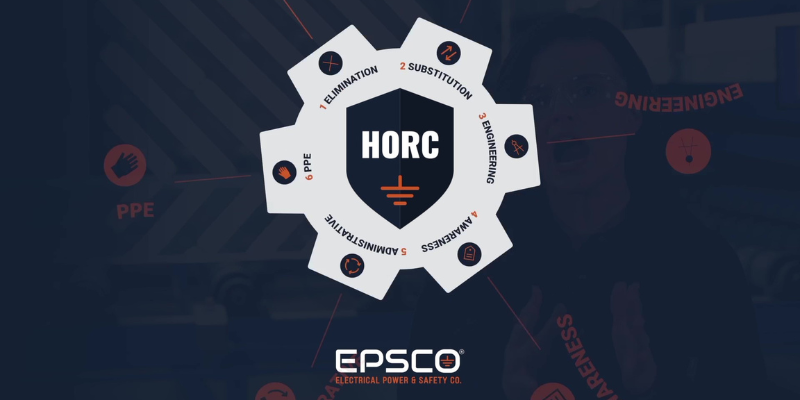
The Hierarchy of Risk Controls
Gaining a good knowledge of your facility is a key component of best safety practices. The more familiar your team is with the equipment, the less likely an accident will occur.
Devising a user-friendly nomenclature that puts everyone at your facility on the same page is one of the most important things you can do.
Naming conventions make a critical difference when it comes to Lock Out / Tag Out and troubleshooting. If naming is outdated on any equipment, use a label maker to update the naming conventions.
If your worksite has multiple services, your team should map out feeds and document which part of the facility each feed services. Confirm that circuit legends in panels and distribution gear are accurate by ensuring labels match the source to the equipment. For example, if the main breaker switchgear is labeled MDP#1, ensure the feed exists and is labeled MDP#1 too.
You’ll also want to inspect equipment for proper settings and maintenance. Make sure spare breakers aren’t left in the ON position so workers are clear about whether the equipment is being used or not. Make sure that there are no breaker blanks in missing panels.
Download EPSCO’s Electrical Safety Audit sheet here
Once you conduct an electrical safety task audit, the next step is preparing your team to deal with potential hazards. Review processes with Qualified Workers to determine how safety can be improved on both an individual and program level. Test and get feedback from everyone on your team so your safety team can develop more helpful training and safety procedures.
At EPSCO, we know getting everyone in your facility on board with the same electrical safety practices is the best way to prevent accidents and electrical fatalities. Be part of our pledge to eliminate electrical fatalities in the workplace by 2030. Conducting an electrical safety task audit at your facility will provide the foundation for your best safety practices.
Don’t forget to subscribe to our blog to get notified when we publish a new article!